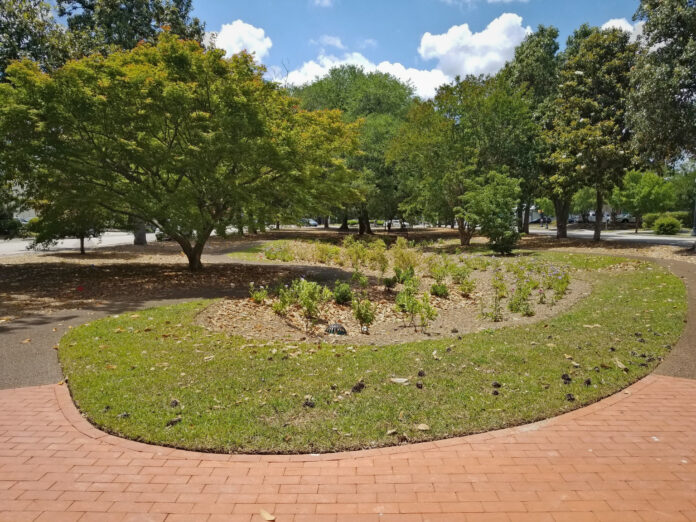
Imagine walking onto a completed construction site. The grass is green; the structures are installed and fencing is in place around the stormwater basins. The contractor’s work is complete, and the Notice of Termination has been filed. Now what?
Stormwater management responsibilities do not end when construction ends, but it does change. Knowing how the site was designed and installed can have a significant impact on the success of the post-construction stormwater quality and the ongoing costs and timelines for the operation and maintenance of the post-construction best management practices (BMPs). Forward-thinking designs and a transition plan to move between construction and post-construction stormwater management ensure long-term success.
Planning for the Future
After the grass grows, stormwater from a regulated site will be subject to ongoing inspections, analytical monitoring and permit-driven water quality criteria, such as being free of debris, odor and floating or settled solids. Post-construction BMPs may reduce discharge volumes, increase infiltration, filter out pollutants and/or direct flow to specific locations on-site, but only if they work as designed. Anticipated post-construction outcomes, operating requirements and maintenance needs should be incorporated into the design during construction planning. While there are initial costs and logistics to be considered during design and construction, there are also long-term considerations.
There are many questions to answer to ensure successful post-construction stormwater management. An owner may
focus on how the site looks, but compliance and operations professionals need to also understand how post-construction controls work.
Transition to Post-construction
During construction, the site changes daily. Exposed sediments may erode and be deposited in basins, inlets and outfalls. Construction materials such as packaging, paints, maintenance fluids and even erosion and sediment control BMPs such as silt fences and containment boxes can leave pollutant residue that have a lasting effect on post-construction stormwater quality. Once construction is complete, the post-construction controls should be clean, new and ready to handle the post-construction land uses.
To reduce cost and improve efficiency, select BMPs that can transition from construction to post-construction applications. For example, avoid swapping out structures such as using corrugated metal pipe (CMP) during construction and CMP during operations. Install the final product, then protect and maintain it during construction. Use temporary controls such as sediment traps and seeding to maintain design flow conditions with minimal transitional maintenance between construction to post-construction activities.
To aid in a smooth transition from construction to post-construction, focus on protecting post-construction BMPs during construction. Block orifices that are not needed during construction and stabilize drainage areas to post-construction inlets. Construction activities should also be sequenced so that a stabilized and completed area is avoided and thereby protected from damage by ongoing construction traffic and storage activities.
The long-term stabilization of a project is affected by proper seeding techniques, correct fertilizers/biotics incorporated in the soil, seed type, seed quality, armoring of the soils and irrigation. Review stabilization criteria in post-construction design plans to ensure the application of the correct materials to get a permanent stand of vegetation. For long-term maintenance, consider an irrigation system as part of the post-construction BMPs for the maintenance of permanent vegetation (Figure 1).
As part of the construction closeout, focus on more than just final stabilization. Removing sediment and other pollutants from the construction site is a key success factor for a good start to post-construction stormwater management. Post-construction controls are designed for anticipated final elevations, flow conditions and pollutant loads. During construction closeout, review as-built conditions to be sure they match design requirements, such as ensuring that the emergency spillway is in the correct location and is sized appropriately.
Longevity, Operation and Maintenance
No material is invincible, so the life cycle of post-construction BMPs must be considered in the design phase. Creating a replacement schedule and critical path items for operation and maintenance can prolong the life and efficacy of post-construction BMPs.
Remember that capital planning is required to replace critical infrastructure. Pavement and basins can become part of the landscape, literally, and are often overlooked in the planning process until something fails to function. Bringing stormwater infrastructure into the business planning cycle helps ensure that there is sufficient budget and lead time to perform updates and replacements.
Designed post-construction BMPs are intended to manage a specific volume of stormwater and pollutant load, so components, including pipe sizes, drainage areas, discharge features, depth, side slopes and filtration media are each calculated to meet the design criteria.
Plant expansions, land use changes, changes in chemical use or manufacturing areas, plus variations in climate patterns may affect the operation of post-construction stormwater BMPs so continual monitoring of operational conditions is necessary to identify the need for updates or adjustments to the design.
Inspection and Maintenance
A comprehensive inspection and corrective action process, along with a schedule for ongoing preventive maintenance will go a long way towards achieving effective stormwater management and extending the life of BMPs. Continual maintenance should include cleaning out accumulated sediments, repairing leaking valves, replacing filtration media and repairing broken elements of the treatment train.
However, design plays a critical part in the maintenance plan. The original design should consider the following items to ensure a successful post-construction maintenance program:
- Access
Fences placed on the top of an embankment structure as a safety measure for pedestrians or mobile equipment can make it difficult for equipment to enter the area to maintain the inside of the pond if the fence is too close to the slope. Overly steep side slopes or unstable slopes in wet weather can further compromise access. Plan to provide a 10-foot to 15-foot (3.1-m to 4.60-m) buffer between fencing and infrastructure, especially along the corners of basins and pipe cleanouts. Provide a shallow side slope to allow equipment access. Provide ladders, steps and handrails to provide safe pedestrian access. Consider the placement and sizing of gates to provide enough room for the equipment to enter.
Access to the outfall is critical and commonly overlooked. The outfall is the point of compliance where monitoring of water quality is measured against permitted limits. Outfalls should be accessible and well maintained. Consider signage, armored walkways and sample structures that allow for safe and easy access for collecting water samples. - Durability
Selecting the cheapest materials can turn into a long-term expense. Corrugated metal pipe corrodes in wet conditions leading to the need to be replaced or lined. Not only does the pipe need to be addressed, but typically the soils surrounding the pipe have eroded, causing voids and potential soil failures that affect other nearby structures, such as roads and fences (Figure 2). - Clogging and Cleaning
When choosing a dewatering structure consider the cleanout methods necessary to maintain the structure. A single-wall corrugated plastic pipe under gravel used as an underdrain in a detention structure for dewatering can easily become clogged, crushed or damaged. Because they are embedded in the bottom of the basin, they are difficult to access and expensive and time consuming to replace or clean. Consider adding cleanout ports or finding an alternative dewatering method to avoid costly repairs. - Aesthetics
Maintenance of items that are both functional and beautiful are often prioritized. Vegetative filters near the front entrance tend to get watered, mowed and maintained, while the outfall at the back end of the pond is overgrown and forgotten. Creative designs that enhance the aesthetics of all BMPs make access to all stormwater features practical and beautiful to encourage ongoing management. - Maintenance Frequency
Selecting BMPs that can be easily and infrequently maintained will lead to better overall management. A good rule of thumb is to seek BMPs that require no more than quarterly to semi-annually (once every six months) can become too expensive to maintain and too easy to strike from a budget. Maintenance measures should be less expensive than a replacement during an enforcement action resulting from a failed post-construction BMP.
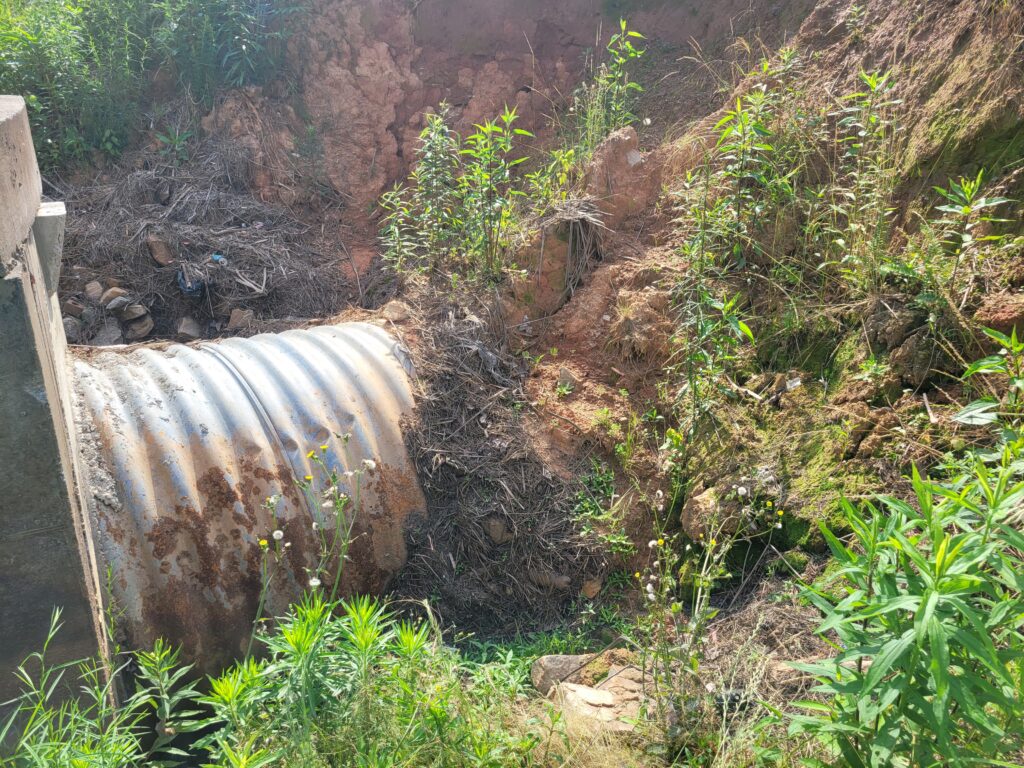
Design criteria, performance and long-term operation and maintenance considerations go hand in hand in making the successful transition from construction stormwater management to post-construction management. A stormwater professional’s knowledge and understanding of how to protect and maintain the hard-won construction project to achieve post-construction stormwater objectives is critical to the success of the site.
About the Experts
- Julie Morelli, PG, REM, CPESC, CESSWI, ENV SP, environmental compliance and regulatory manager at H-E-B, has been a stormwater professional for 25 years in the consulting industry. She has worked with stormwater and water quality issues in construction, industrial and municipal settings.
- Susan Yates, CPESC, CESSWI, environmental compliance manager, Real Estate Department, Southeastern Freight Lines. She has been a stormwater professional for 25 years and has worked in regulatory, consulting and the private sector as an environmental and stormwater manager.