The Challies Island Bridge project by Matt Taylor, Operations Manager at Taylors Contracting in Nelson, New Zealand, involved the construction of a 30 m (98.5 foot) moveable bridge across the Waimea River at Challies Island in the Tasman District near Nelson (Figure 1).
The bridge allows 80 t (88.1 ton) laden, rigid dump trucks to cross the river and transport gravel from a nearby extraction site for processing without vehicles having contact with the water, thus eliminating sediment discharge. The bridge can be removed in 48 hours if a major flood is predicted. It was manufactured by the engineering company Eastbridge.
Gravel extraction commenced at the Challies Island site in the early 2000s. Originally, this effort consisted of articulated dump trucks (ADTs) crossing the river using truck wheel washes to minimize sediment movement. This effort progressed to ADTs crossing the river via culverts installed for them. Neither approach was ideal, as sediment was generated to varying degrees. Taylors did not consider this approach environmentally sustainable or a best management practice (BMP), and it was not how it wanted to operate as a business. At this stage, a removeable bridge was proposed.
Like many regions around New Zealand, the Tasman region has a list of infrastructure projects that require aggregate. As demand for development increases, there will be increasing pressure to acquire aggregate.
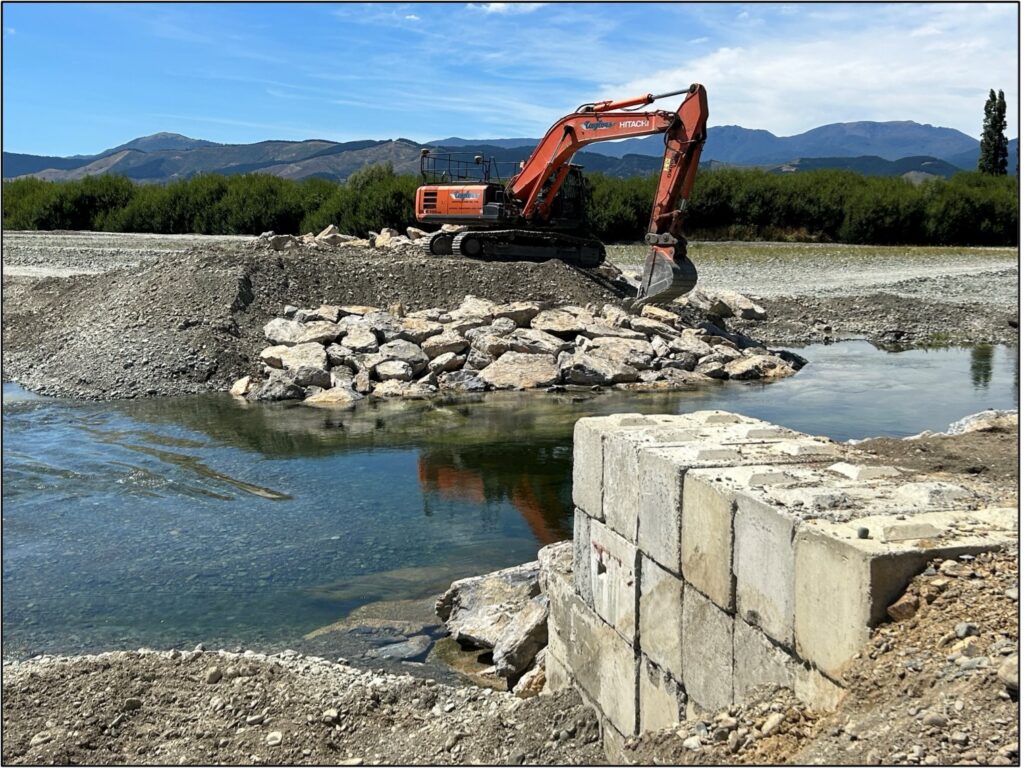
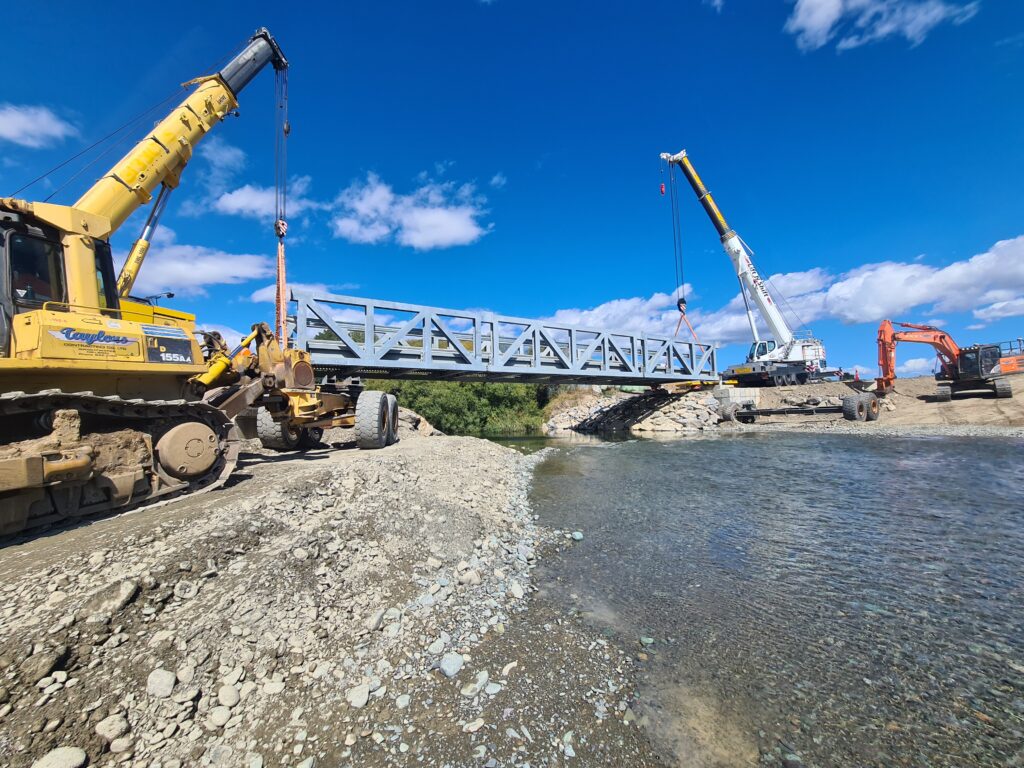
Designing and building the bridge enabled the client to process material into aggregate. It also provided access to alluvial aggregate, which is better suited to concrete and asphalt production as it has been weathered and any soft rind removed. The resulting hardness produces structurally sound concrete. Adverse effects on the environment were minimal, if any existed, creating a win-win for all stakeholders.
Reverse Engineering the Solution
Importantly, the Challies Island project was “reverse engineered” starting at the river and working back.
The bridge design and construction required high-level problem-solving and creativity. The bridge itself was supplied in sections and assembled on-site. This work was undertaken under a high level of public scrutiny and within view of a large volume of commuters using a major road nearby.
The team was presented with four large truckloads of modular components at a total of 70 t (77.1 tons). The drawings, consents and the challenge began. Abutments were constructed from both sides, which removed the need for crossing flowing water, thus eliminating disturbance of the river (Figure 2).
Once the abutments were constructed and compaction testing completed, the next challenge was lifting and placing 70 t (77.1 tons) of steel across a flowing river. A set of wheels was constructed for both ends. By working from both sides, an access ramp was constructed beside the abutments. A crane was positioned on each side to lift. The bridge was transported across the river in one move, which created minimal disturbance (Figure 3).
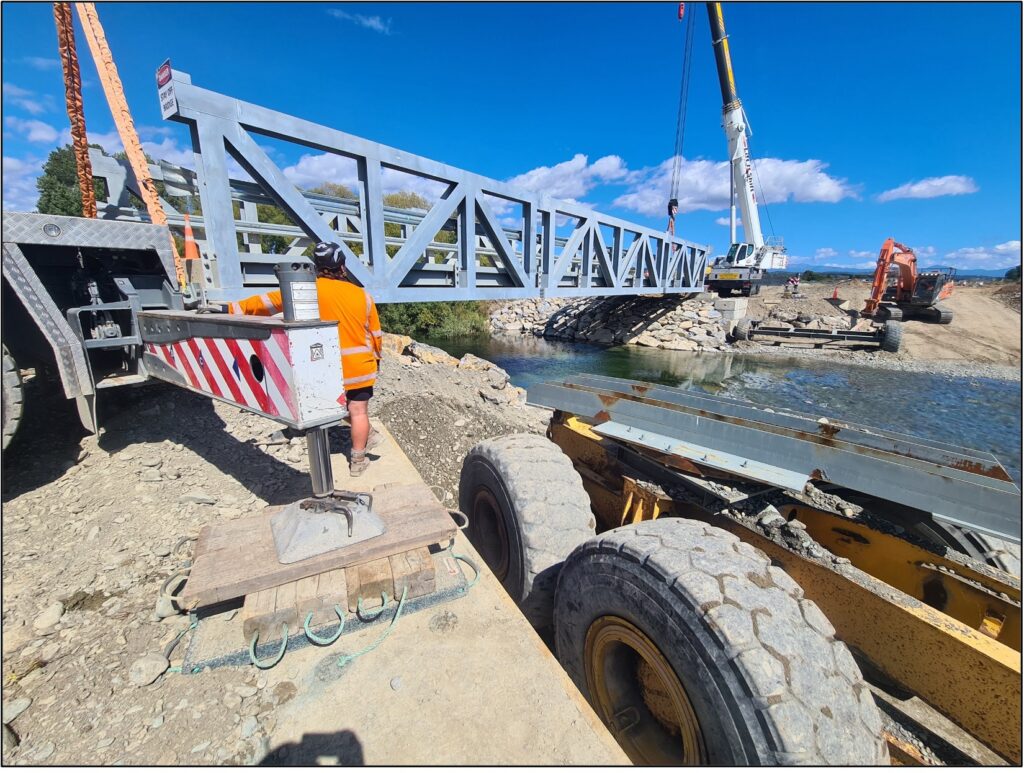
Designed With the River and Other Users in Mind
The bridge is designed and installed with the dynamic river flows and resource consent requirements in mind so as to not create erosion of the riverbed. During design and installation, attention was also given to other river users so as not to create a navigational hazard (Figure 4).
The contractor is responsible for resource consent compliance during a forecast flood event, which stipulates the bridge must
be removed if the temporary foundations become compromised. A construction emergency action plan was developed and refined after each large rainfall event and elevated river flow.
How Do You Put This Together?
Assembling the bridge on-site meant there was no level concrete floor to work on and all the equipment had to be mobile. The contractor had to prepare a working site, which involved levelling and compacting the gravel area within the Waimea River Park berm land.
Once assembly commenced, it was difficult to get the holes lined up to connect the sections. The workshop team needed to be innovative and developed pins to mock up the sections and then fit the bolts. There are about 1,000 bolts that are 30 mm (1.18 inch) diameter holding the bridge together. The bridge took approximately six weeks to assemble.
Once it was assembled, the bridge needed to be moved. This need provided an additional quandary, as it was too big and heavy to put on a truck. Trucks would also sink in the river gravel under the weight. The workshop team suggested fabricating dollies that would sit under each end of the bridge. These were made using old dump truck chassis, with one having an old excavator ring so the bridge could be turned and manoeuvred more easily.
The bridge allowed for the transportation of excavated gravels across the river while leaving the water flowing clear. There was no requirement to introduce fish passage systems as would have been required with the temporary use of pipes.
During a couple of raised river flow events, the dry secondary overflow channel was activated. This step allowed the bridge to remain in place due to the flow being split between the bridge and the secondary overflow channel. Removal could have introduced environmental risk by generating sediment and placing machinery in a vulnerable position during rising river levels. This outcome has been good as it created minimal disturbance and discharges to the receiving environment (Figure 5).
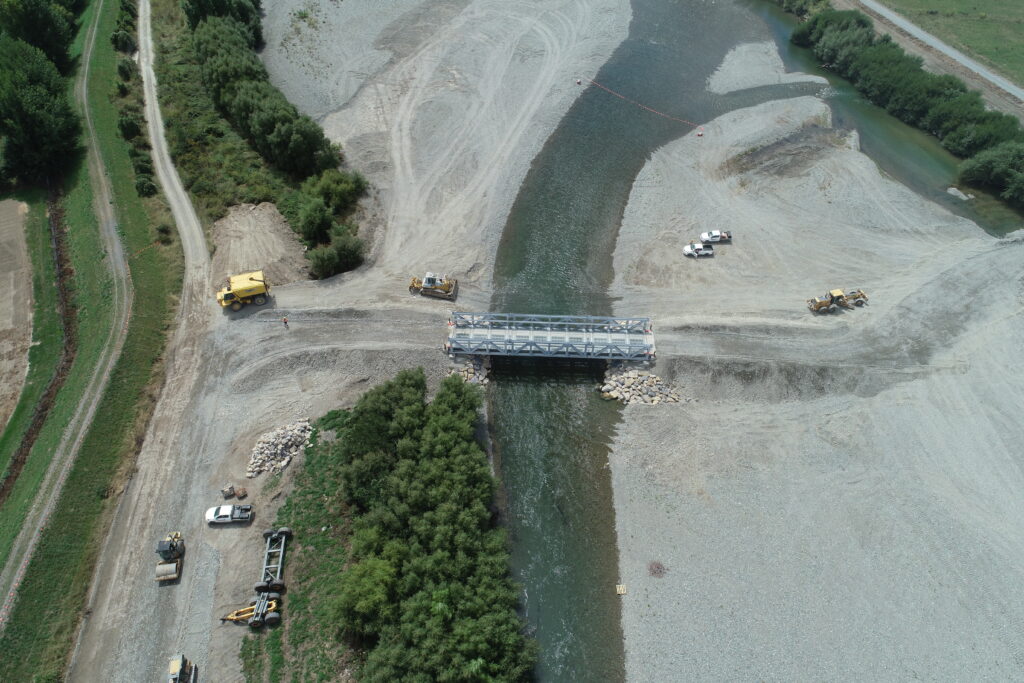
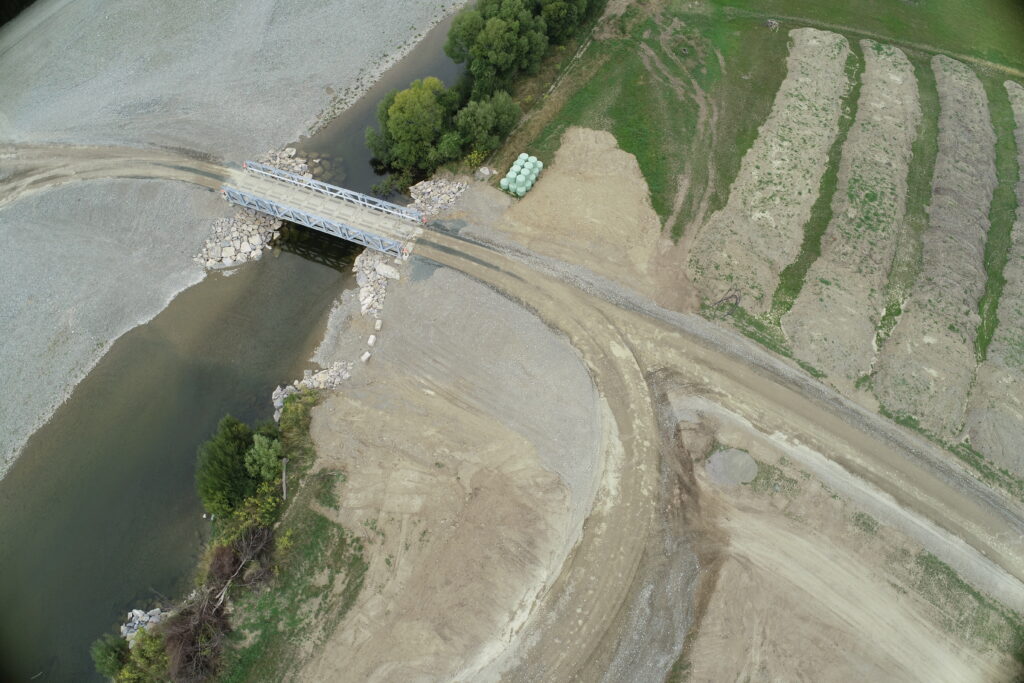
Meeting Community Expectations
There is ongoing community sensitivity about gravel extraction. Diligent communication was needed with the community about the methodology being used. Noise and dust needed to be proactively managed to stay within required consent limits. Full compliance has been achieved to date, and a robust relationship has been maintained with the regulators.
To help achieve compliance, an automatic monitoring system was installed at the site. This system monitored noise, dust and weather (wind speed, temperature and direction), which enabled prompt decisions to be made when unfavourable conditions were detected. Mitigation measures were put into action to prevent any adverse effects on the environment, neighbours or the community in general.
Regular communications were made with compliance staff, and site visits were encouraged to monitor the progress of the project.
Upon completion and once cartage was completed, the bridge was removed in reverse to the installation. The river gravel abutments were spread and large rock was removed, which left no footprint. Full regulatory compliance was achieved.
Setting the Benchmark
Gravel extraction can be managed so that it is compatible with, and even beneficial for, river control. It can also assist with the restoration of wildlife habitat.
The removeable bridge is seen as a solution to the issues presented by historic gravel extraction because it minimises the footprint of gravel extraction and its effects on the environment. The key to the ongoing success of the project is this minimal environmental impact combined with a willingness by the civil construction industry, landowners and the Tasman District Council compliance team to work together and find a resolution to any percieved or actual issues (Figure 6).
This project exemplifies the thinking and innovation that goes into designing solutions that meet the needs of communities and our environment while enabling access to the resources we need to keep vital infrastructure projects moving forward (Figure 7).
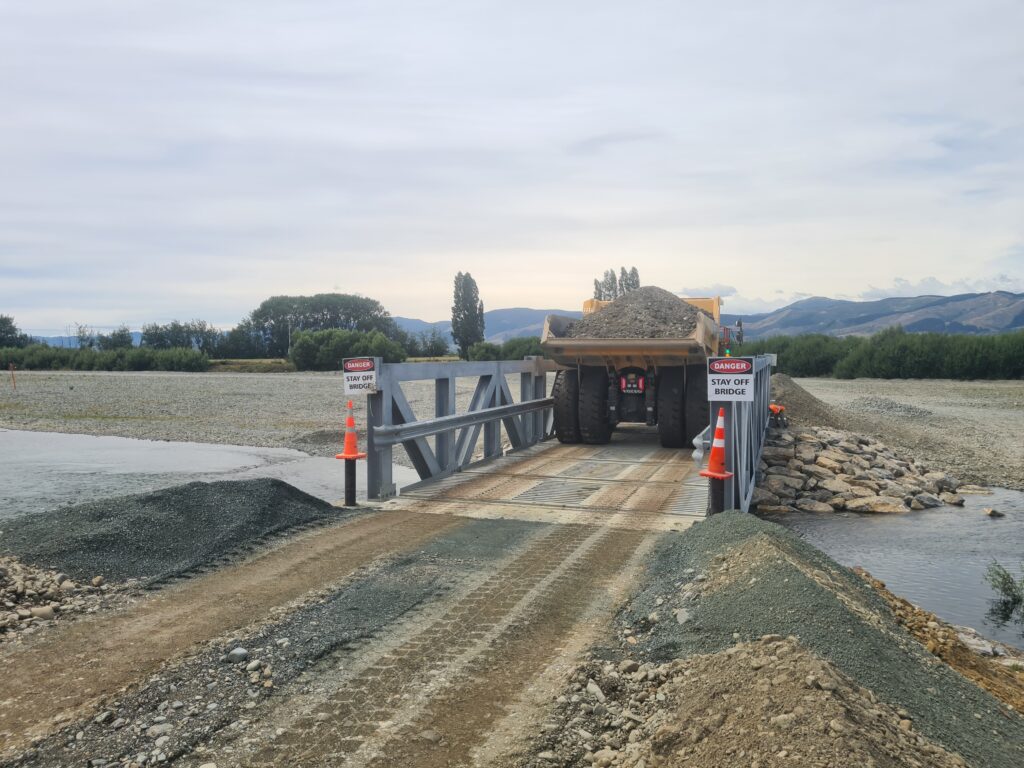
About the Expert
Matt Taylor is Operations Manager for Taylors Contracting, established by his parents in 1971. Matt’s ability to design fit-for-purpose equipment and processes has been the hallmark of the business for 53 years.