One of the most common sediment management problems on construction sites is mud deposited on roads by vehicles, commonly referred to as “track-out,” as they leave the site. The most common practice to prevent track-out is a construction site driveway consisting of large rock that is supposed to knock the mud off the tires, though little research exists on how effective these exits are. In recent years, an increasing number of reusable track-out prevention methods have been created and marketed as a better, more sustainable alternative to the stabilized construction exit. These products can be easily cleared of the sediment they collect, unlike the stone exits, which require either top dressing with additional stone or removal and replacement of stone for maintenance.
Research Objectives
This research aimed to determine the efficacy of three track-out prevention systems as affected by differing soil properties.
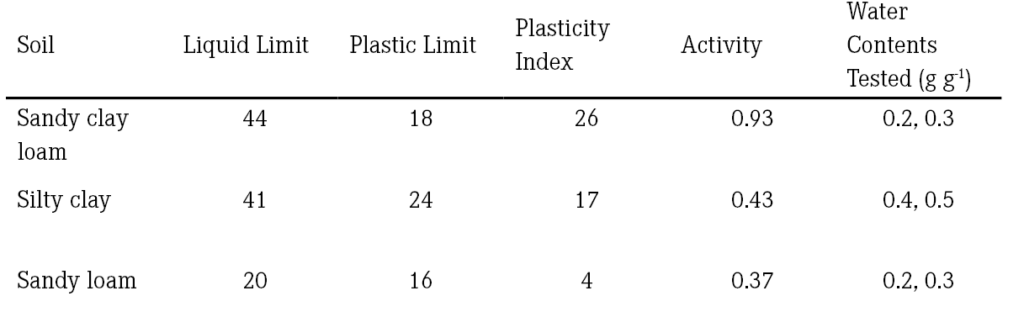
Methodology
Testing was conducted using three track-out prevention methods: a standard stone exit constructed using class A stone, a FODS Trackout Control Mat and a RubberForm Trackout Control Mat. The prevention methods were built or installed according to North Carolina Department of Transportation and manufacturer specifications, except the length of each was only 14 feet (4.3 m) as opposed to the standard 50 feet (15.2 m) used for stone exits. During testing, sections of muddy tire made four contacts with each prevention method over a total distance of 28 feet (8.6 m), a little over half the length of a full-sized exit. Additional testing using eight contacts was also conducted to determine if the results from the initial testing were transferrable to longer lengths.
Testing was conducted using three soils, each at two water contents determined in lab testing to be the “stickiest” for each texture. Water contents are listed on a mass basis, with units of g g-1 indicating the mass of water per mass of soil used to create the mud, with higher values generally indicating a thinner mud (Figure 1). The plasticity index is found by subtracting the plastic limit from the liquid limit and describes the range of moisture contents over which the soil deforms plastically. The activity is calculated by dividing the plasticity index by the clay-sized fraction of the soil, and there is an established relationship between clay mineralogy and activity values. Higher plasticity index and activity values suggest increased potential “stickiness.”
Tires were cut into 14-inch (35.6-cm) sections, and pre-portioned mud was evenly distributed to a 12-inch (30.5-cm) long portion of each tire section. The mud was uniformly pressed into and over the tread of the tires using a metal spatula. These tire sections were then attached to a vehicle tire and driven over a given prevention method to produce four or eight contacts (Figure 2). Mud removal was determined by weighing the tire sections before and after testing.
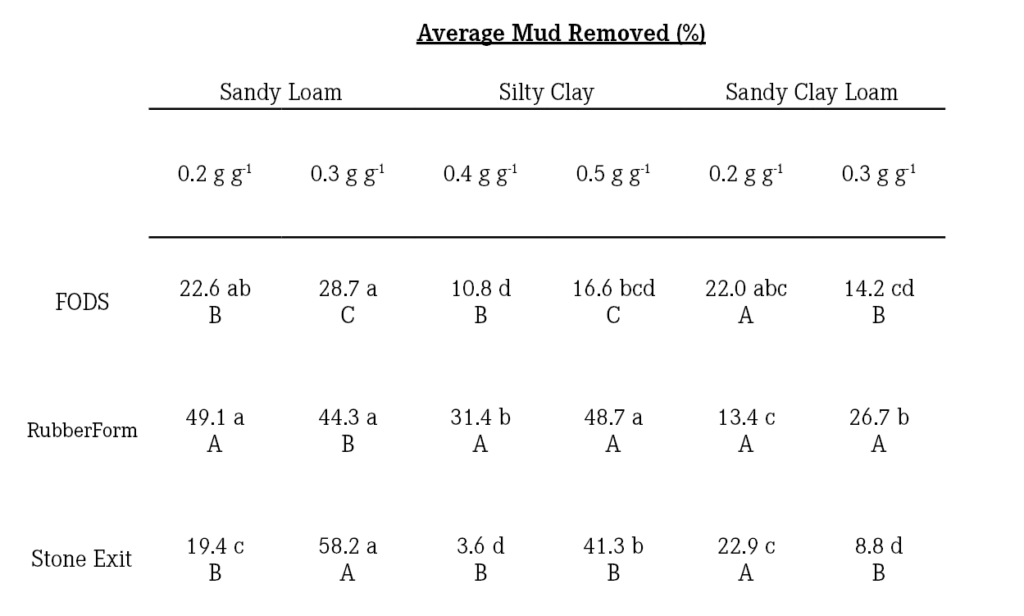
Findings
When the effect of soil condition on prevention method effectiveness was considered, FODS Trackout Control Mat performed best with sandy loam at both water contents and sandy clay loam at 0.2 g g-1. The RubberForm Trackout Control Mat performed best with both water contents of sandy loam as well as silty clay at 0.5 g g-1. The stone exit performed best with sandy loam at 0.3 g g-1 and silty clay at 0.5 g g-1.
The highest average mud removal for any device after four contacts was 58.2% when sandy loam at 0.3 g g-1 was used on the stone exit (Figure 3). This is contrasted by the lowest average mud removal (3.6%), which also belonged to the stone exit, with silty clay at 0.4 g g-1. The FODS Trackout Control Mat had the narrowest range of average mud removal — the most consistent performance, followed by RubberForm Trackout Control Mat and the stone exit, with 17.9%, 35.7% and 61.8%, respectively. It is also important to note that while the stone exit did have the highest average mud removal for one condition during testing, the exit was freshly installed and was not heavily trafficked. The situation in this testing gave the stone exit its best possible outcome, though this may not be indicative of heavily trafficked exits on active construction projects. It is also noteworthy that the stone exit gave the least consistent performance across soil conditions (i.e., the widest range of mud removal).
When testing was conducted with a subset of soils and the contact number was doubled from four to eight, only the stone method had a proportional increase (2X) in mud removal. The stone exit removed more than double the amount of silty clay at 0.4 g g-1 when the contact number was increased from four to eight, 3.6% and 8.1%, respectively, but in both cases, mud removal was relatively low (Figure 4). While FODS Trackout Control Mat had significant increases in mud removal with increased contact numbers for both water contents of silty clay and RubberForm Trackout Control Mat had significant increases in mud removal with increased contact numbers for sandy loam at 0.3 g g-1, neither of these devices had proportional increases in mud removal (Figures 5 and 6). This suggests a diminishing return on mud removal with extended lengths of track-out prevention methods.
Conclusion
Track-out prevention is an important part of reducing offsite sedimentation on construction projects. Soil texture, water content and clay type (i.e., activity) all impacted the effectiveness of the prevention methods. While all methods tested in this study had a measurable impact on mud removal, no method consistently removed more than 50% of mud from vehicle tires. This suggests that the “shaking” approach to removing mud from vehicle tires can be relatively ineffective across a variety of soil conditions and types. In most cases, doubling the number of contacts did little to improve performance.
This diminishing return on mud removal indicates that increasing the length of a track-out device may not solve the issue of track-out. With the traditional stone exit widely used on many projects, there is a need for continued innovation to produce a more consistent and still economical method to remove mud from vehicle tires across a range of soil conditions. Track-out testing was intended as a controlled comparison of soil conditions on track-out devices. This research should not be interpreted as a direct quantitative representation of track-out device performance on active construction sites.
References
- ASTM. 2017. Test Methods for Liquid Limit, Plastic Limit, and Plasticity Index of Soils (D4318-17). ASTM International. https://doi.org/10.1520/D4318-17E01.
Acknowledgments
This research was supported by the staff and faculty at North Carolina State University. The North Carolina Department of Transportation sponsored the research. FODS LLC and RubberForm Recycled Products LLC provided their track-out control mats to be used in this research. The findings expressed in this article are those of the authors and do not necessarily reflect the view of the sponsors.
About the Experts
- Karina Lenko completed her master’s degree in soil science at North Carolina State University (NCSU).
- Christina Kranz, Ph.D., is a lecturer at NCSU.
- Rich McLaughlin, Ph.D. is an emeritus professor at NCSU.
- Joshua Heitman, Ph.D., is a professor of soil physics at NCSU.
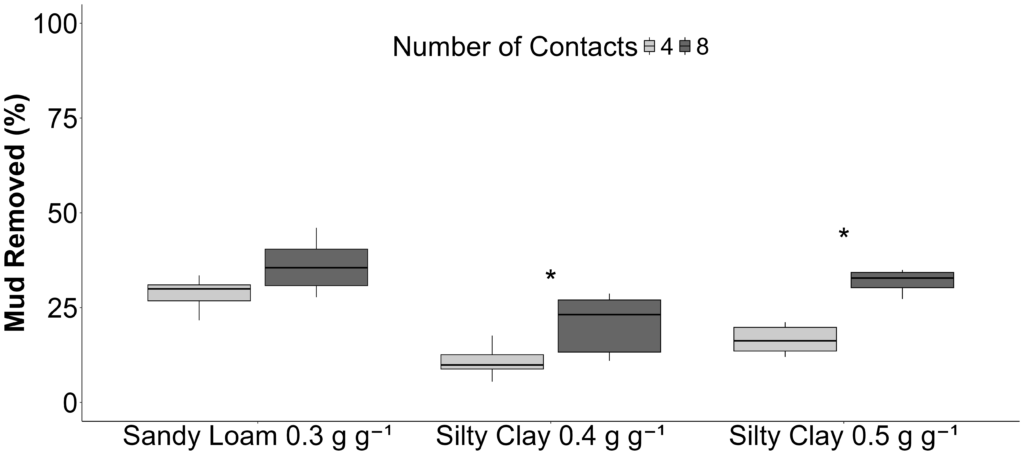
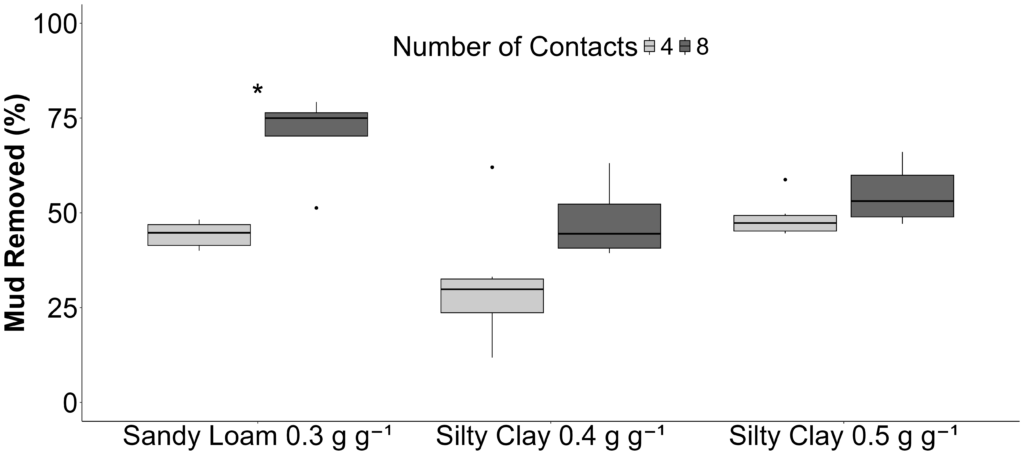
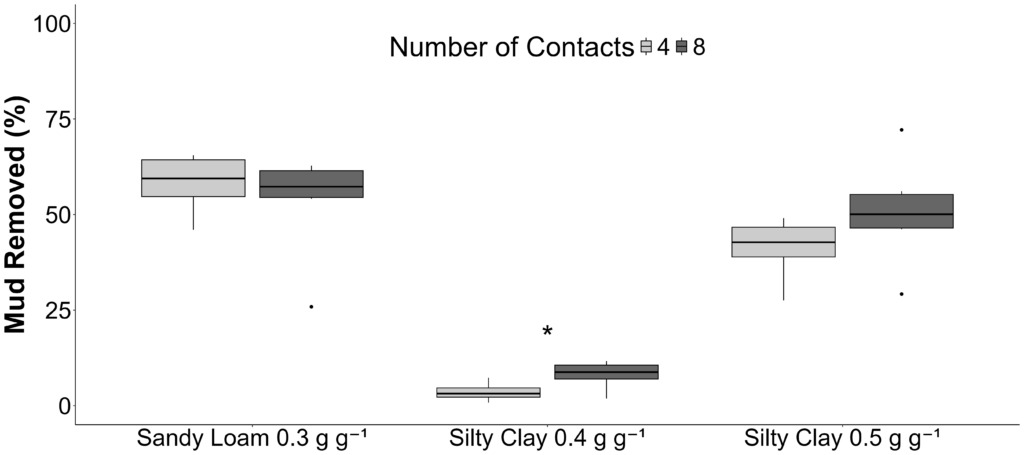