A site contractor has a three-fold objective:
- Produce a quality product.
- Finish the job on time.
- Don’t lose your profit.
Difficult to do, but possible if unexpected problems do not arise. It is a safe bet that unexpected problems will present themselves, especially as the job approaches completion. Removing sediment from a pond is one of those problems that no contractor wants to address.
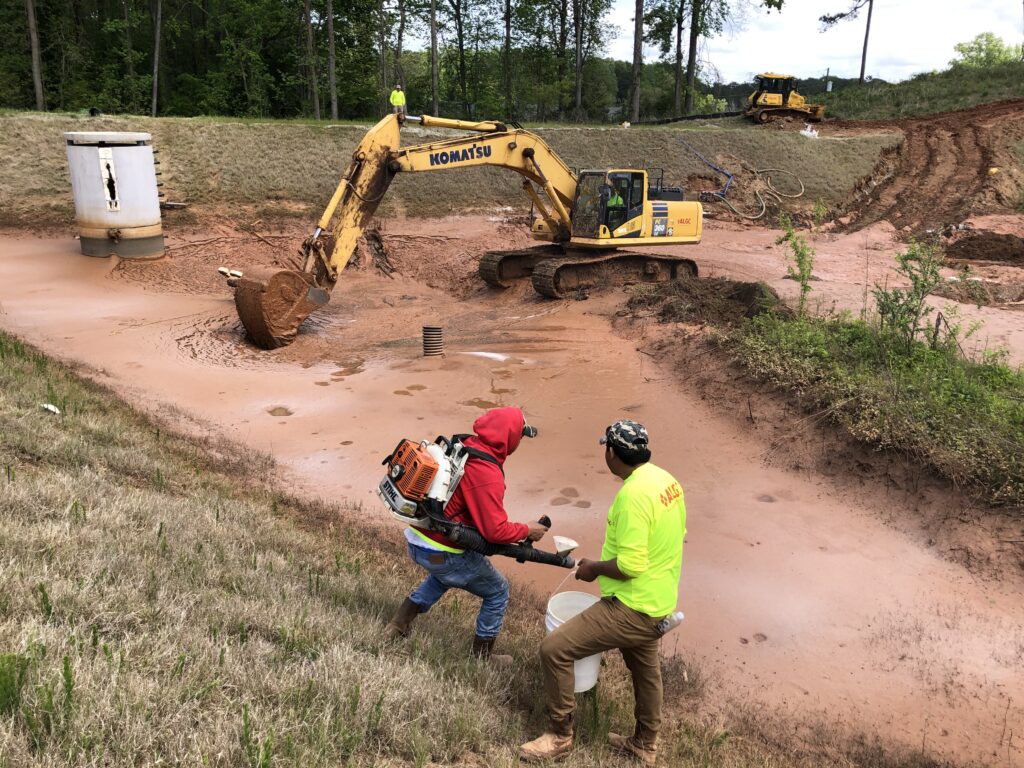
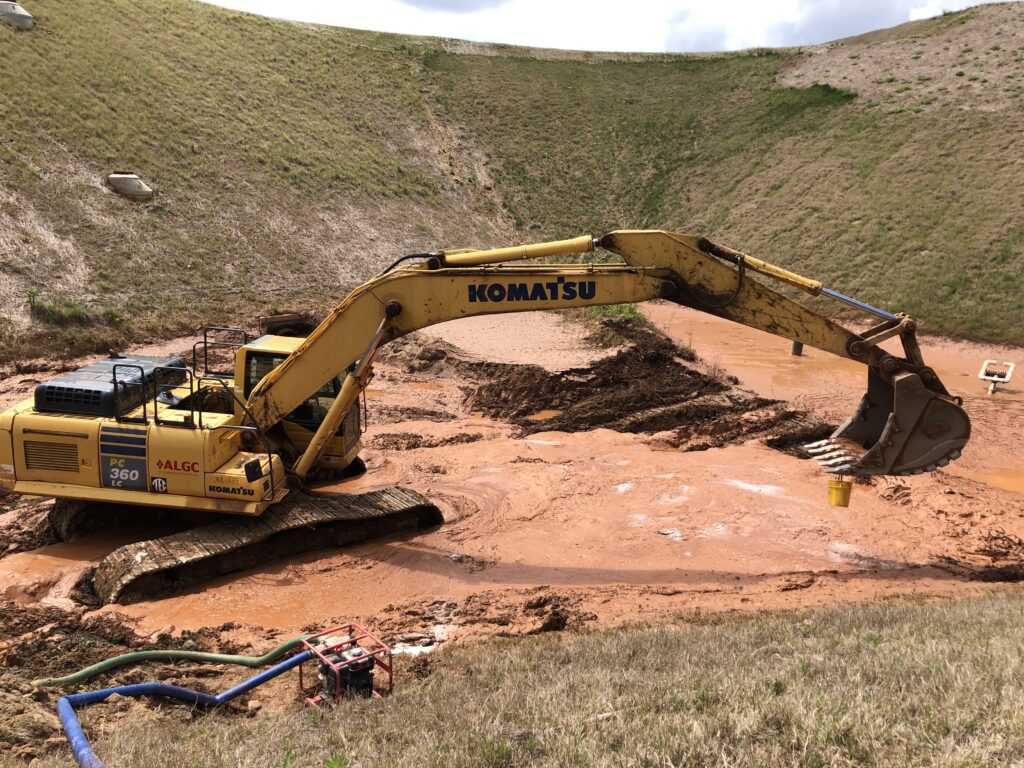
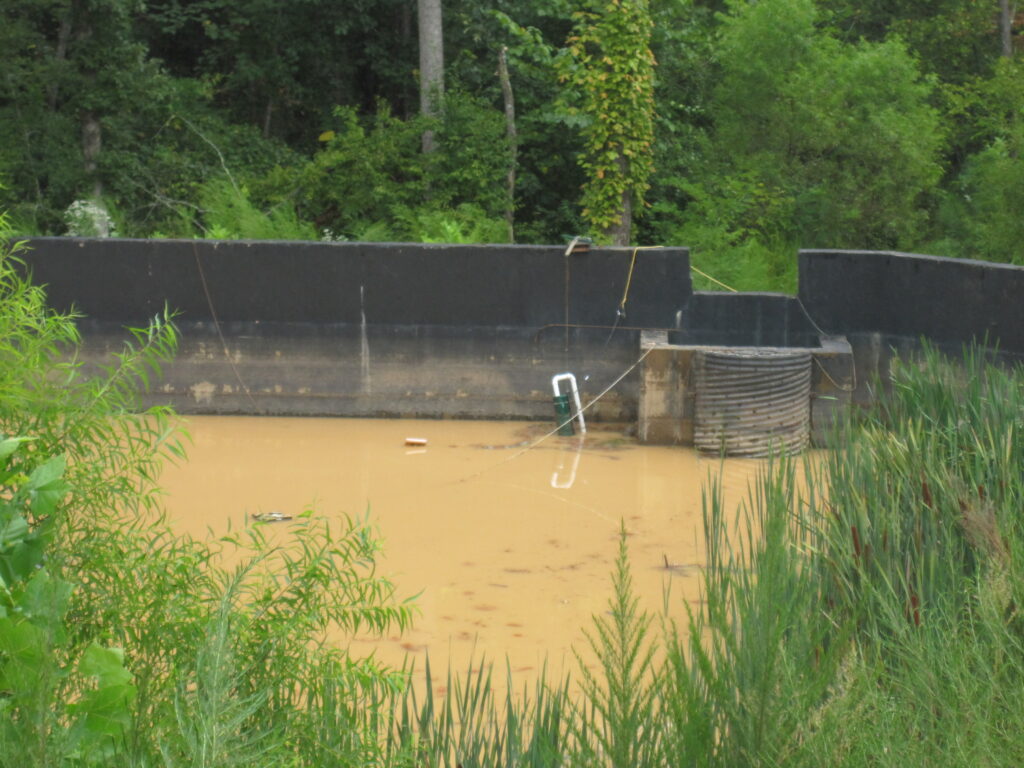
Sizing Up a Problem
Some construction sites do not have sediment pond management problems, at least not for a while. Soon enough though, the fine sediment seals the underlying soil pores, and infiltration is restricted.
Other sites have a lot of clay in the soil. These cohesive soils do not provide good infiltration. From the onset, they retain all of the inflow. As the water level approaches the maximum pond designed capacity, operators begin to wonder about dewatering them because contractors want to capture sediment, not to store water. Many pond systems include a dewatering device to achieve this goal. At the end, the contactor still faces a volume of soupy sediment that must be removed. Sediment in large ponds can be hydraulically dredged and piped to another area. Small ponds are more commonly treated with a polymer, which binds fine soil particles together, to change soupy sediment into a semisolid that is removed with mechanical equipment.
Four different options to address sediment pond management were used in the following construction projects in Georgia:
- The Hawthorne Project
The Hawthorne Project pond (Figure 1) is one of several constructed to retain sediment on a new, large housing complex site. It was constructed over a buried water line. The sediment had to be removed from the pond before the water line could be removed. Grading was nearly complete, and the site plan did not identify any nearby location where the soupy sediment could be deposited when pumped out of the pond.
An effective solution to this problem was to block the discharge from the pond. A backpack leaf blower distributed a mixture of polymer and sand over the surface of the sediment (Figure 2), and an excavator mixed the polymer into the sediment (Figure 3). After one more application and mixing, the sediment changed from a liquid to a semisolid that could be loaded and transported by the contractor’s earthmoving equipment. The mud was spread and allowed to dry. - The Meadow Walk Project
Construction was approaching completion at the Meadow Walk Project, and soupy sediment needed to be extracted from the pond to meet the designed volume criteria. An anionic powder polymer was mixed with sand into a bucket having holes in the bottom. An excavator was used to swing the bucket over the pond. The bucket was then used to incorporate the polymer/sand into the slurry. The treated sediment was transformed into a semisolid mass that was loaded and trucked from the site. This two-step process required only a few days to complete. - The Parkway Point Project
The turbidity of water in the pond at the Parkway Point Project exceeded the regulatory discharge standard. A shut-off valve was installed at the outlet control structure of this pond to stop discharge from entering a wetland. A simple closed-loop system withdrew water from the pond, passed it over blocks of polymer in a corrugated pipe and returned the polymer treated water back into the pond. Sediment settled in the stagnant pond. The surface water met the standard and was allowed to be discharged by a surface removal system. - The Sixes Project
Using a nearby source of electricity, a submersible pump lifted turbid water (Figure 4) and dropped it into a vertical pipe containing a block of polymer (Figure 5). The treated water was discharged back into the pond. One week later, the water was released (Figure 6). No maintenance was required.
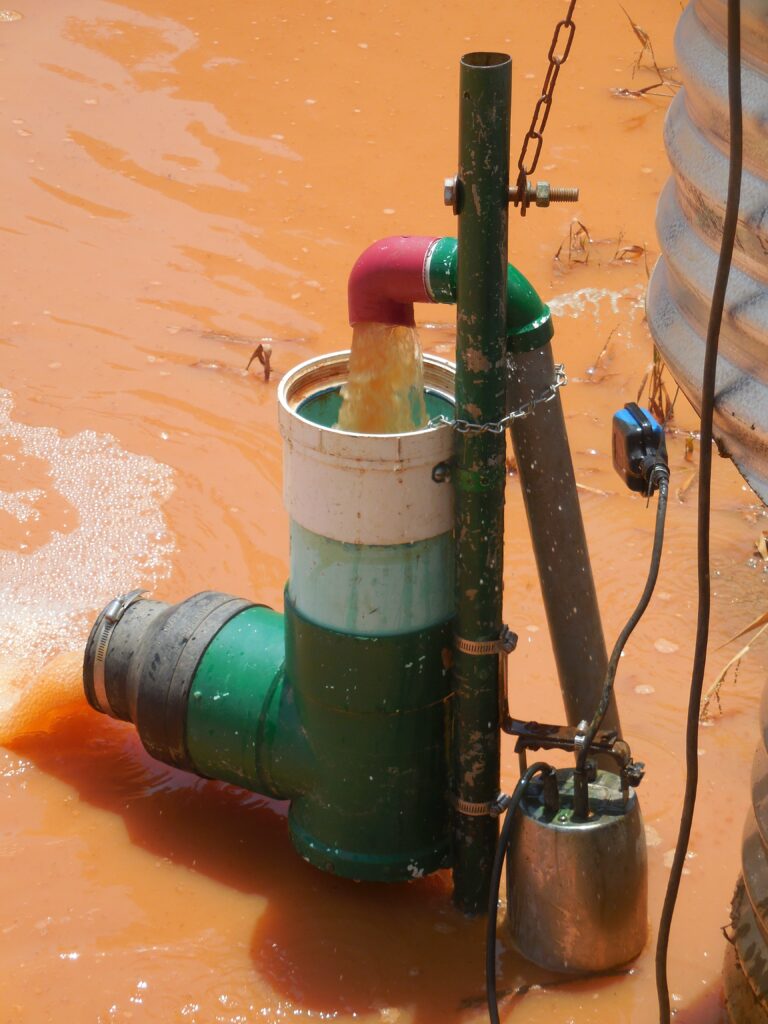
Lesson Learned
On another construction site polymer-treated sediment was pumped into a filter bag. Instead of releasing the water, the bag retained the soupy sediment. It is thought that the polymer treated sediment clogged the bag pores and restricted water release. The pump pressure was so great that the bag quickly filled and the seams failed. Polymer-treated water flowed down the slope and into a stream. The lesson learned: When combining two or more BMPs, be sure to understand the interaction and limitations.
[Editor’s Note: This is the third and final article in a series that addressed the use of polymers for erosion control on jobsites. Previous articles appeared in the third quarter 2023 and first quarter 2024 issues of Environmental Connection.]
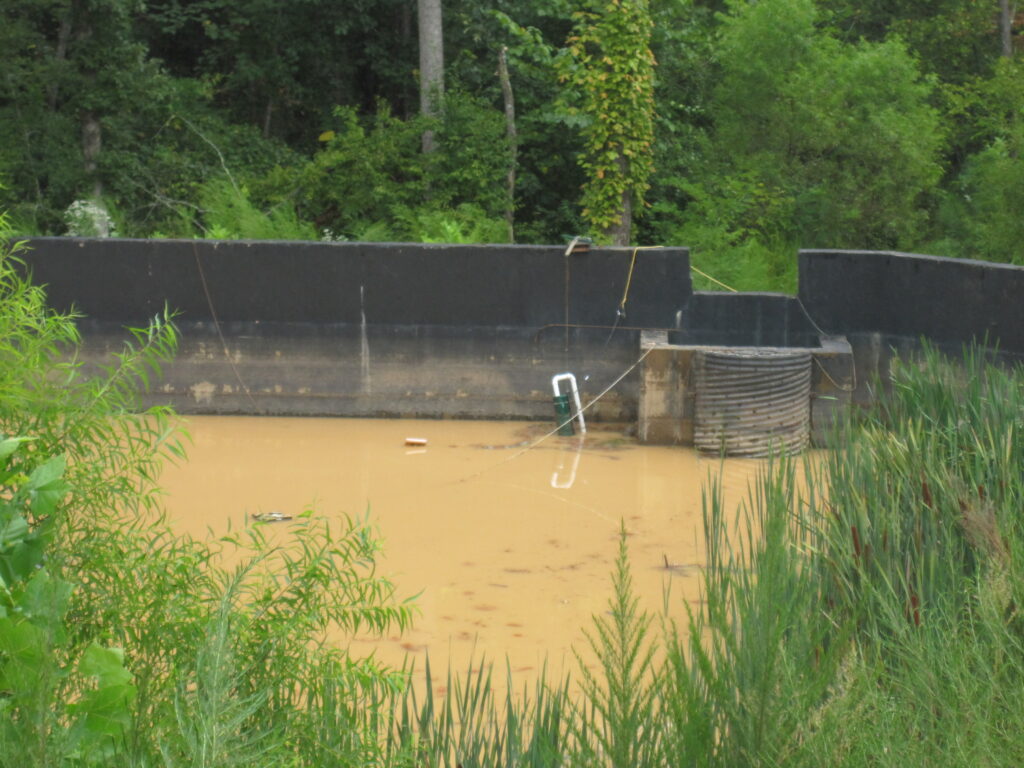
About the Expert
James W. Spotts, Ph.D., CPSS, CPESC, is president of Southeast Environmental Consultant LLC. His company assists contractors with environmental problems during construction. He also provides site inspections and NPDES discharge monitoring in the regional Atlanta area. Also known as “Dr. Dirt,” he is a long-time member of IECA and is passionate about teaching others how to solve field problems.